How it all works.
Safely.
Welcome to our planned
underground mine.
It will be the first underground mine in Minnesota since the closure of Ely’s Pioneer Mine in 1967. Its surface impact will be 80% smaller than a traditional open pit mine of similar production capacity. And, we’ll be mining between 400 feet and 4,500 feet beneath the surface.
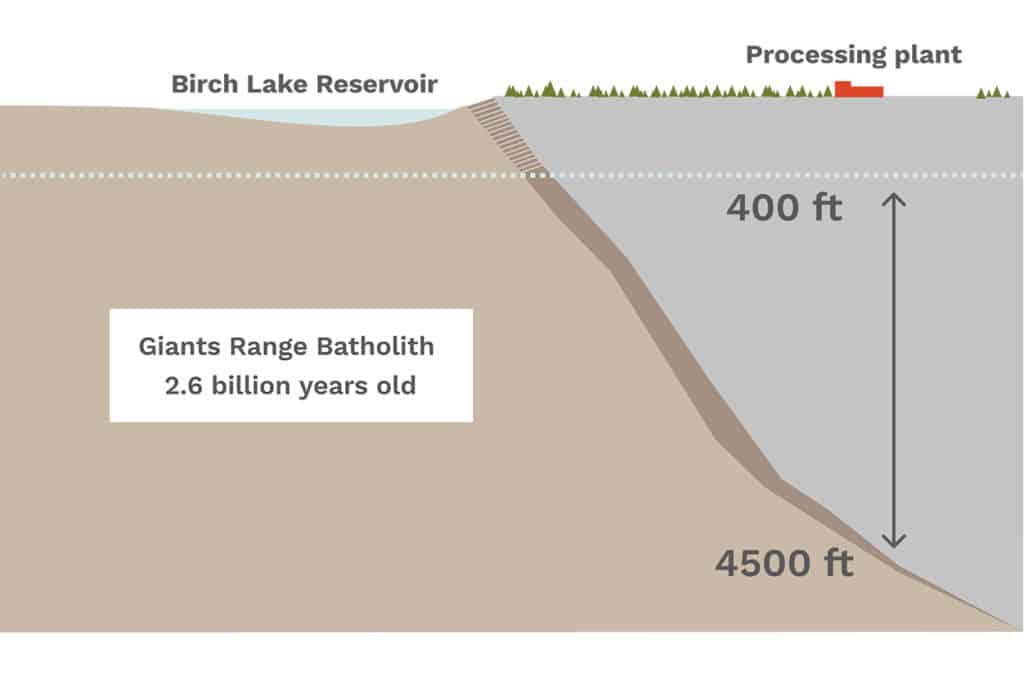
Now comes some of the advanced technology.
We already know the minerals that are in the deposit — copper, nickel, cobalt and platinum-group metals. Not only that, we know precisely where they’re located. In fact, we have a large number of core samples as a library of the deposit’s exact location. Our core storage facility in Ely houses 1.5 million feet worth of core samples that we have drilled from the deposit over the past decade; another half million feet of samples are at state storage facilities.
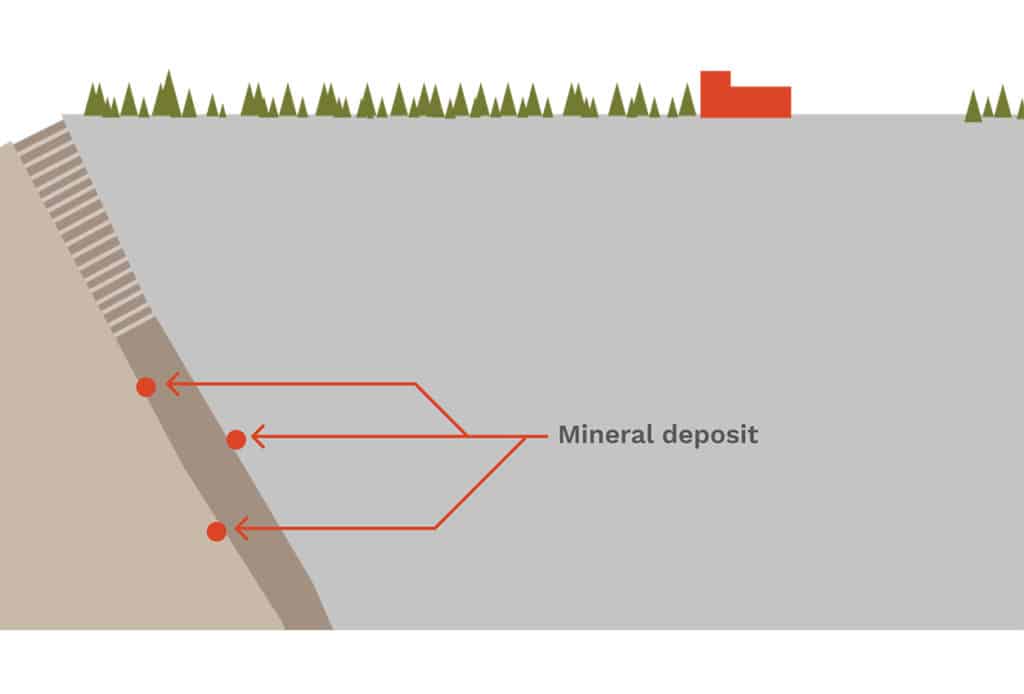
So how do the miners get to these depths?
This is also the beauty of an underground mine. First we bus mine employees to the site from Ely and Babbitt to minimize local traffic. The mine workers will then be transported by bus down to the mine in one of two 1.25 mile tunnels. No more lowering miners down a shaft. Plus the underground mining areas are well-lit and ventilated with accommodations like break rooms and offices.
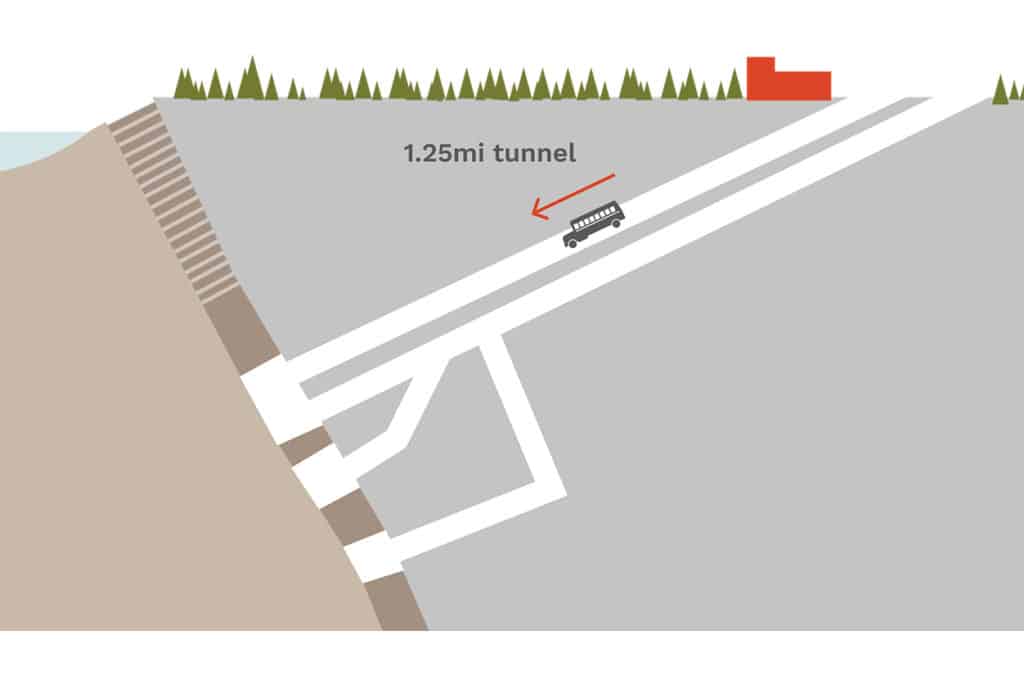
Then comes the mining.
This happens in areas called stopes or rooms that are opened through drilling and blasting. The ore containing the minerals is then crushed underground, which minimizes project impacts by containing noise and dust deep beneath the surface. A conveyor belt in the second tunnel then transports the crushed ore to the processing plant.
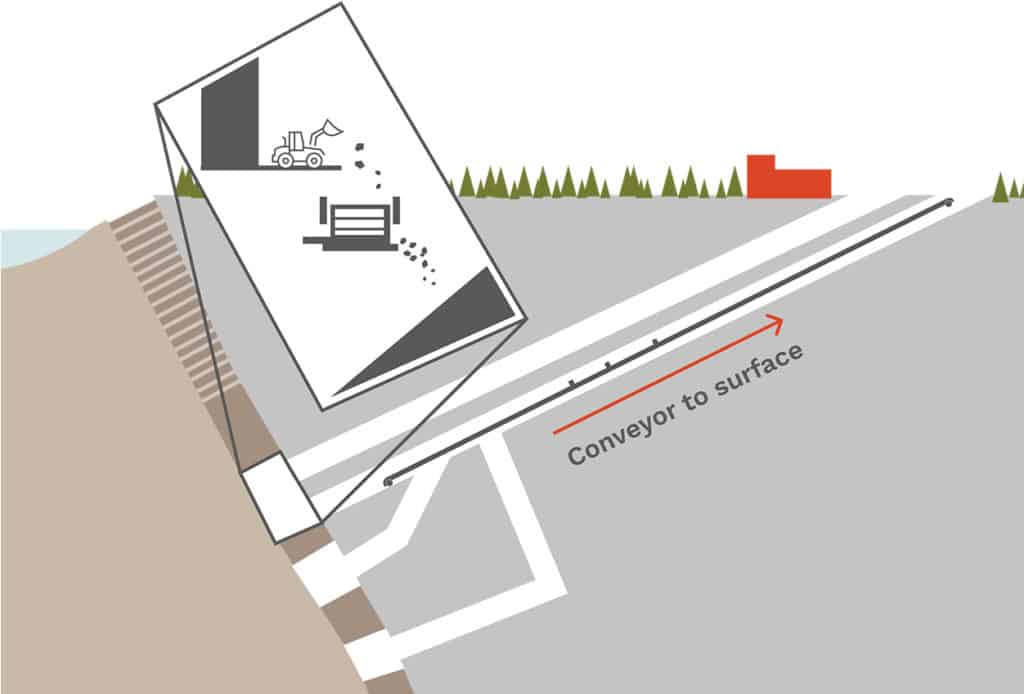
Back above ground.
At the processing plant, the metals will be extracted from the crushed ore through a flotation process. Once extracted, the mineral concentrate is placed in sealed shipping containers on semi-trucks. Water used in the concentration process will be reused on site in a closed-loop system — another technological advancement that helps protect the environment.
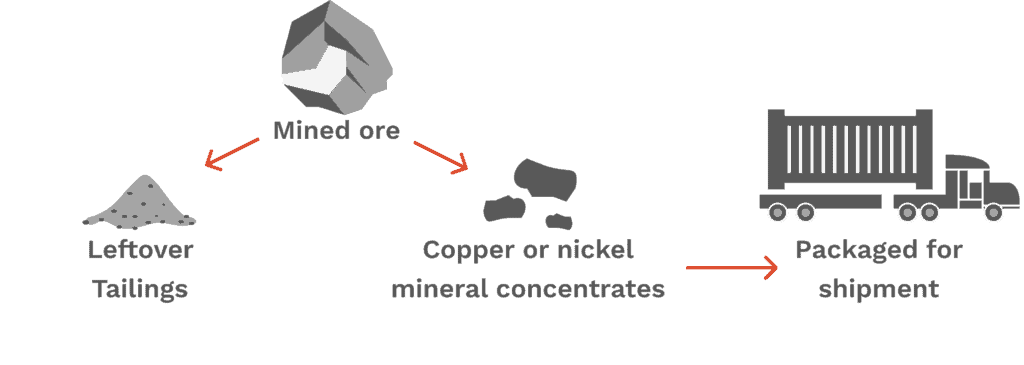
What about the leftovers?
When you extract minerals from ore, “tailings” are left over. By having an underground mine, up to half the tailings will be stored back underground in the stopes as cemented backfill. This helps stabilize the mine during and after production. The other half will be compacted into a dry stack mound and concurrently reclaimed with native soil and vegetation. No tailings dams are necessary, completely eliminating any risk of a dam failure.
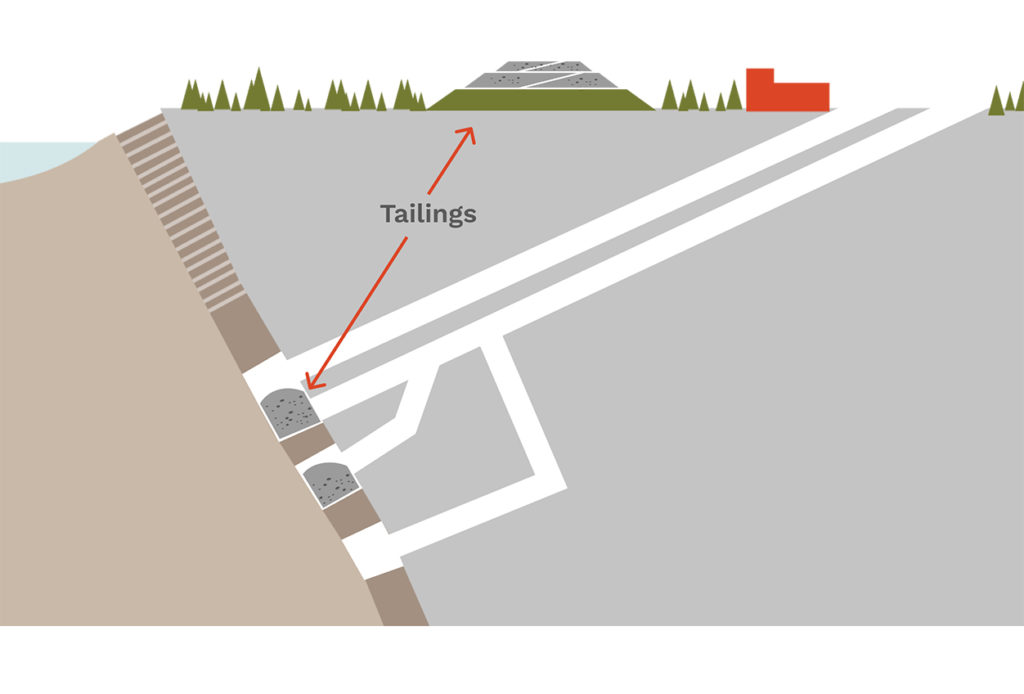
A word about acid rock drainage (ARD).
Because of the geology, as well as our mining method, the tailings produced will be non-acid generating — meaning no ARD. The remaining sulfur left in the tailings after the minerals are removed does not meet the threshold for acid generation. Twin Metals has tested its tailings for more than a decade to confirm this using the International Network for Acid Prevention’s Global Acid Rock Drainage Guide.
Read the full white paper and executive summary about our project’s lack of ARD potential.
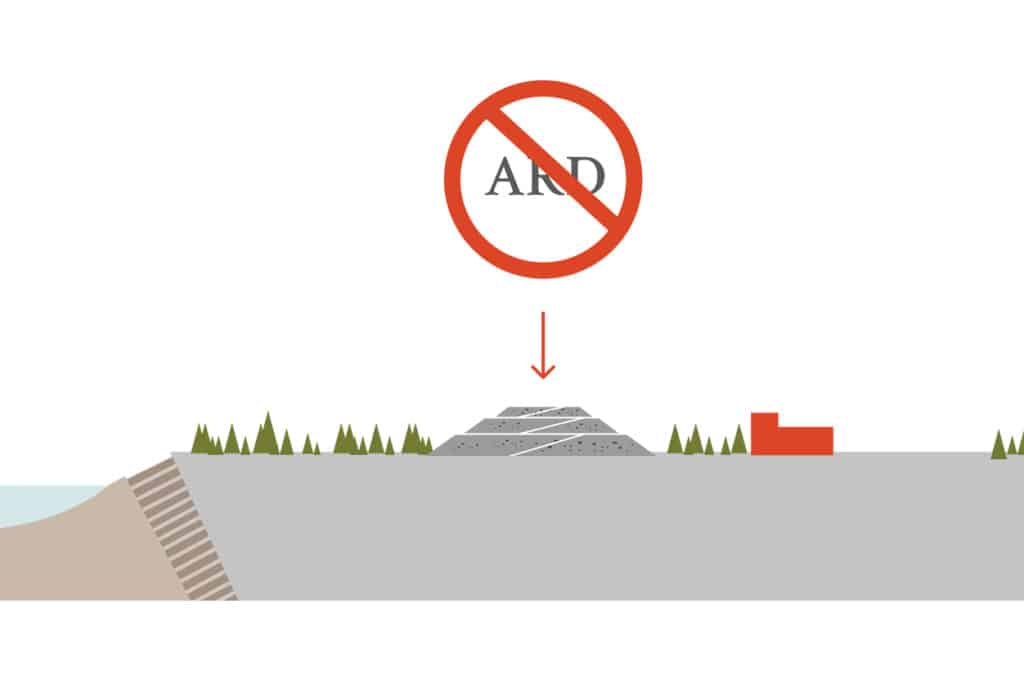
The closing.
When the project is complete, the majority of the surface infrastructure will be removed from the site. The area will be reclaimed with native soil and plantings in order to return it to a natural state reflective of the surrounding topography. The underground mine facilities will be sealed. Reuse of the land after project closure will be determined at a later date.
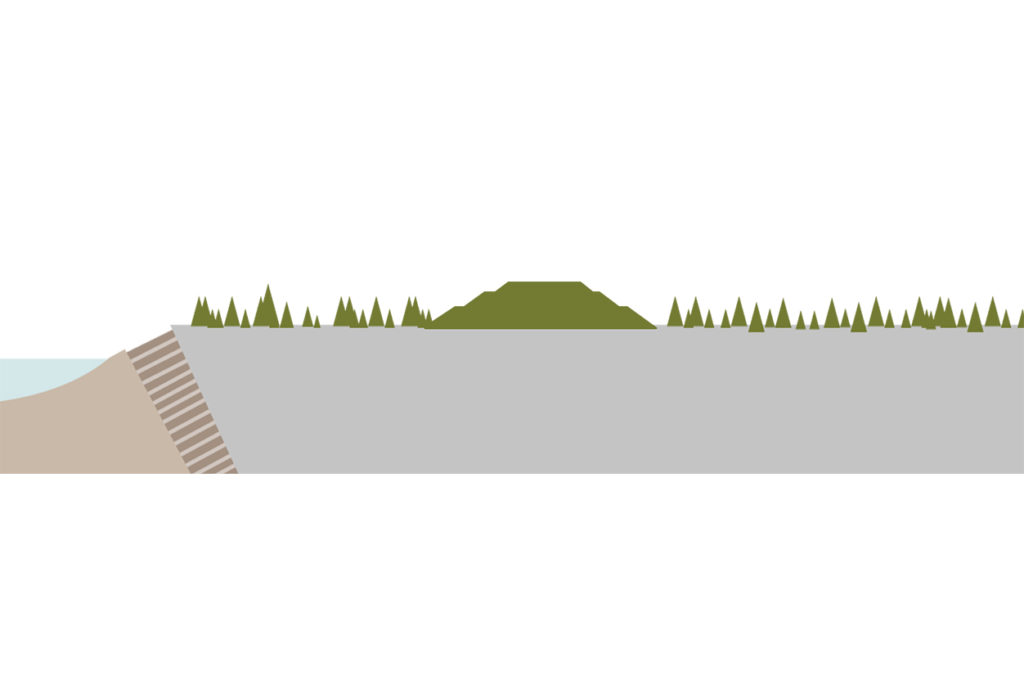